SLC | S21W3 | Costs for entrepreneurs - Costing methods
Hello everyone! I hope you will be good. Today I am here to participate in Steemit Learning Challenge of @yolvijrm about the Costs for entrepreneurs - Costing methods. It is really an interesting and knowledgeable contest. There is a lot to explore. If you want to join then:
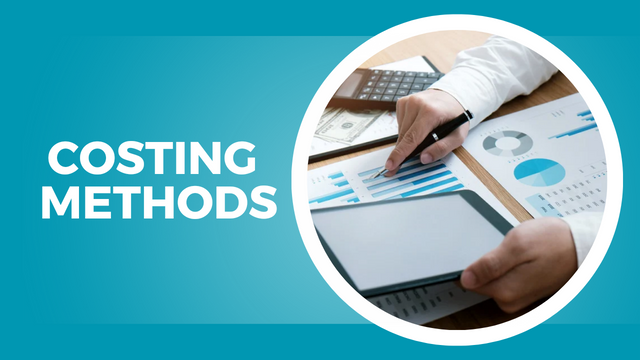
What are costing methods and what is their importance?
Costing methods are the techniques which are used by the business. The businesses determine the costs for the production of the goods or to deliver services by using these costing methods. These methods help the companies to assess the expenses involved in the production. They include labour, materials and all other overhead costs. Common costing methods are given below:
- Job Costing: This costing method is used for the unique and custom products or the services. These costs are tracked on the basis of the job or project completion.
- Process Costing: This costing method is applied when we are dealing with the mass production settings. In this mass production identical units are produced. The costs are calculated by calculating the average across all the units.
- Activity Based Costing: This costing method allocates overhead costs on the basis of the specific activities which are related to the production.
- Standard Costing: This costing method is used to set standard costs for the materials and labour. It also includes overhead costs. It sets standards by comparing them with the actual costs for the variance analysis.
- Marginal Costing: This costing method is used to determine only variable costs. It helps in decision making by ignoring the fixed costs in the short term price decisions.
- Absorption Costing: This costing method is used to allocate variable and fixed costs for the product units. It is often required for the financial reporting.
Importance of Costing Methods
Costing methods are important for many reasons:
- Profitability Analysis: These help to determine the true cost of the products. They enable accurate strategies for the determination of the price and profit.
- Budgeting and Planning: Costing methods help for the budget formulation. They help to allocate the resources by predicting the costs.
- Cost Control: They help to identify the cost driving factors where can implement cost saving measures.
- Inventory Valuation: Costing methods ensure the proper valuation of the inventory. It is essential for financial statements and tax purposes.
- Decision Making: These methods help to make decisions on the expansion of the products. They help to reduce the cost and operational inefficiencies.
- Performance Evaluation: These costing methods compare actual costs with the standards or budgets. They highlight the variance in the performance.
Explain the difference between the job order and process costing methods.
Job Order Costing and Process Costing both methods are used to track production costs. But they are different in their application based on the nature of the production.
Job Order Costing
- Definition: Job Order Costing method is used when the products are manufactured on the basis of the specific orders by the customer with the different requirements.
- Application: It is commonly used in construction industries. It's application can also be found in the custom manufacturing and services such as legal or consulting firms.
- Cost Accumulation: The costs are tracked individually for each job or project. The costs are recorded separately for each job such as direct materials, labour and overhead costs.
- Costing Objective: It calculates the cost of each individual job. It provides a transparent picture of the profitability on the basis of each job.
- Example: A furniture company which produces custom pieces will use job order costing. It will assign specific costs to each custom product. The cost will be assigned solely based on the materials, labour and requirements of the client.
Process Costing
- Definition: Process costing method is used in the mass production environments where the similar units are produced continuously.
- Application: This method is used in the food processing and oil refining industries. It can also be applied in any manufacturing process where there is a continuous flow such as in the chemicals, paper and cement.
- Cost Accumulation: In this method the costs are accumulated for each process for a specific time period. Then these costs are divided on all the units produced in that period.
- Costing Objective: This method calculates an average cost per unit by dividing the total process costs by the number of units produced. It is useful for the consistent and high volume production.
- Example: A soft drink manufacturer will use the process costing to determine the cost per bottle. It will be done by averaging the total cost of ingredients, labor and overhead over all bottles produced in a batch.
Key Differences
Aspect | Job Order Costing | Process Costing |
---|---|---|
Type of Production | Custom, unique jobs | Mass, continuous production |
Cost Tracking | Costs tracked per individual job | Costs tracked per process or department |
Industries Used | Custom manufacturing, service industries | Manufacturing with repetitive processes |
Cost Calculation | Each job has its own distinct cost | Costs are averaged over all units produced |
Costing Purpose | Calculate specific job costs | Calculate average cost per unit |
Each method provides valuable insights for different types of production. It allows the companies to manage the costs effectively according to their production processes.
Research and explain, to the best of your understanding, two costing methods different from those explained in this class.
I will discuss Target Costing and Kaizen Costing. These are valuable in the specific business context. Both the methods highlight the cost control. They are often used in those environments which focus on the continuous improvement and where the price strategies are set based on the customers.
Target Costing
- Definition: Target costing is a strategy to set the prices where the price of the target products is determined on the basis of the desired profit margin. And this is the price which the market is willing to pay. This method is commonly used in those industries where the prices in the market are competitive. The companies use this method to manage the costs to meet the specific profit goals.
- Application: It is widely used in those industries where the companies need to set competitive prices for the new products. For example automotive and electronics manufacturing.
- Process: In the target costing target prices are set for the products by maintaining the desired profit to reach at a target cost. And the company works to produce the products within the cost. They follow optimised processes, reduce waste and do not source cheap materials.
- Objective: The goal of the target costing is to ensure that costs remain within the target range. It is kept in mind to not sacrifice the quality of the products. It enables the company to remain competitive while achieving the goals of profits.
- Example: If an electronics company is launching a new smartphone and it determines that the target market price is $700. If the company wants to keep the desired profit margin of 20% then it will produce the phone for the $560 which becomes 80% of the target price. In this way target costing method helps companies to adjust the production costs according to the target price in the market.
Kaizen Costing
- Definition: Kaizen Costing method is a cost reduction and improvement approach. It is based on the Japanese philosophy of continuous improvement. That is why the name of this costing method is Kaizen. It focuses on achieving the small and incremental cost savings over time. It does not set the fixed cost targets.
- Application: This costing method is commonly used in lean manufacturing environments. Consumer goods manufacturing industries are best examples of these environments. Because in these industries continuous optimisation of the process is important.
- Process: In Kaizen costing the costs are reduced through the small improvements in production processes. Costs are also reduced by managing the employee practices and materials used. In this approach collaboration from all levels of the organisation is required. In this costing method employees are encouraged to find the opportunities to save the cost.
- Objective: The primary objective of this method is to achieve cost savings of the products without compromising the quality. This method helps to continuously improve the cost efficiency.
- Example: In the car manufacturing plant Kaizen costing is suitable. It involves minor adjustments to reduce the material waste. The Kaizen method will streamline the processes of the assembly line. And it will help to gradually decrease the production costs with respect to time.
Summary of Key Features
Costing Method | Target Costing | Kaizen Costing |
---|---|---|
Focus | Setting and achieving a specific target cost | Continuous cost reduction and improvement |
Primary Goal | Meeting a target cost to stay competitive | Incremental cost savings without reducing quality |
Industries | Electronics, automotive | Manufacturing (especially lean environments) |
Cost Control | By designing products to meet a predetermined cost | Through small, ongoing process improvements |
These methods allow businesses to manage costs strategically, whether through price-driven targets or gradual efficiency improvements, fitting well within competitive and lean production contexts.
Perform the costing by work orders, according to what was explained for a cake manufacturing business
To perform costing by work orders for a cake manufacturing business using the Job Order Costing System I will break down costs into direct and indirect categories.
Here’s a structured example:
Cake Manufacturing for a Custom Order
Determination of Direct Costs
- Ingredients (Direct Materials): This includes direct raw materials such as flour, sugar, eggs, butter, etc. These can vary based on the specific cake order.
- Labour (Direct Labour): I will calculate the hourly wage of the baker for the time spent on cake order.
I have determined these costs as follows:
- Ingredients cost: $40
- Labor rate: $20/hour
- Time required: 3 hours
Direct Costs Calculation:
- Direct Materials: $40
- Direct Labor: $20 x 3 hours = $60
- Total Direct Costs: $40 + $60 = $100
Determination of Indirect Costs
Indirect costs include rent, utilities and equipment. These can be allocated to multiple work orders. For example:
- Equipment costs: Oven, mixers, utensils (amortized over many orders)
- Utilities: Gas, electricity
- Other overhead: Rent for the bakery space
I am taking total indirect cost for six months as $6,000. And the bakery completes an average of 120 orders in that time which becomes 20 orders per month. According to this:
Overhead Allocation per Order:
- Total Overhead: $6,000
- Total Orders: 120
- Allocated Overhead per Order: $6,000 / 120 = $50
Calculation of the Total Cost per Cake Order
I will add direct costs and allocated indirect costs to get the total cost for this custom cake order.
Cost Component | Calculation | Total |
---|---|---|
Direct Materials | Fixed at $40 | $40 |
Direct Labor | $20 x 3 hours | $60 |
Indirect Costs | Allocated overhead | $50 |
Total Cost | $150 |
The total cost to produce this cake by following the Job Order Costing System is $150. This cost includes all necessary components. We can set a selling price based on this minimum cost by considering the desired profit margins.
I would like to invite my friends @patjewell, @hudamalik20 and @enamul17
Greetings @mohammadfaisal
1.- You have explained the costing methods as a set, which is nothing more than the specific procedures used to determine a cost, pointing out at the same time some of the most common ones and the importance of them.
2.- You have pointed out the difference between job order costing and process costing, indicating the specific differences in them and how both are linked to the way of production.
3.- You have explained two other types of costing such as activity-based costing and kaizen costing, an efficient and useful Japanese method. You have detailed some aspects of operation and the mechanism of working with these costing methods.
3.- You have indicated the elements used in the manufacture of cakes, and segregated each of them according to their classification, which has allowed you to determine the cost and production of a cake.
Thanks for joining the contest
Spending decisions need to focus not only on numbers, but also on long-term planning.
Good luck for the contest.
Yes you are right the vision of every business is to focus on the king term planning and growth.