Modification of the trays valves, evaluation of the operational conditions of a absorption column
Greetings scientific community and friends of Steemit in general, welcome to my engineering blog. Today we will be dealing with an issue related to an operational problem presented in the hydrocarbon processing industry, specifically an extra heavy crude upgrader occurred in an absorption column with amine during the gas sweetening process.
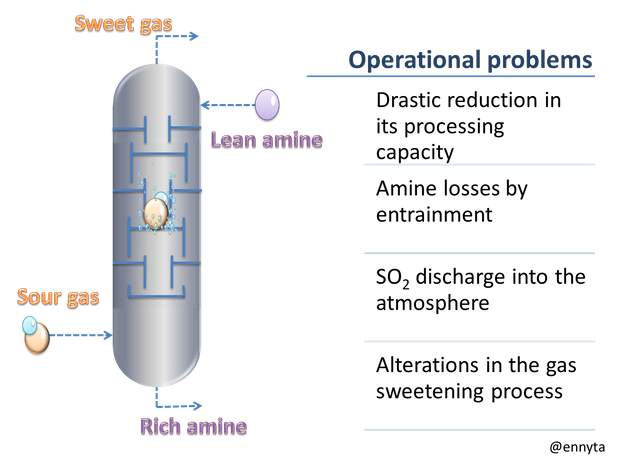
The purpose of this paper is to study the gas sweetening through the process of absorption of H2S with amine to obtain a fuel gas that complies with the environmental and operating regulations of the extra heavy oil upgrader. The simulation software PRO/II was used for the compositional evaluation and Sulcol for the hydraulic evaluation. The absorption column presented problems related to amine losses, discharge SO2 into the atmosphere and deficiency in the gas sweetening process.
It is assumed that these limitations were associated with fouling of the trays, consequently causing clogging in the movable valves. According to the problems presented by the column, it was decided to modify the original design of the movable valve trays and convert them into fixed valve trays at their maximum opening, using welding as a means to carry out this purpose.
.gif)
Operational problems related to the clogging of the movable valves [Design created by the author @ennyta]
The main objective was to evaluate the operational conditions of the absorption column in its new adaptation. Simulation models were developed so as to know the percentage of absorption efficiency of H2S in the gas as well as the hydraulic conditions in the column. Additionally, it was sought to optimize the key parameters which belong to the gas sweetening process through a sensibility analysis, in order to operate with the correct flow rate at an adequate MDEA concentration and avoid hydraulic limitations. In addition, the opening of the valves was evaluated as a recommendation for improvement alternatives.
As a result, the minimum flow conditions of the column were determined and the use of amine was optimized using a minimum concentration of 30% w/w of MDEA, reducing 15% w/w in reference to the design conditions. It was demonstrated that the gas-liquid rate in the column was not correct during the operations which directly affected the efficiency of absorption of H2S in the gas. In relation to these problems, the case studies did not comply with environmental regulations with absorption efficiency lower than 70%. The case with movable valve trays presented more loss of amine; for this reason, it was demonstrated that, for dirty systems such as delayed coking unit, it is more favorable to operate with fixed valve trays and in accordance with the evaluation results, at a valve opening of 70% to avoid problems related to the hydraulics and the weeping phenomena. Later we will be analyzing these results.
This research seeks to assist in the achievement of effective, economical and environmentally sound operation. To reduce investment costs in terms of the acquisition of new trays for the column as well as the replacement of MDEA due to amine losses.
What is gas sweetening?
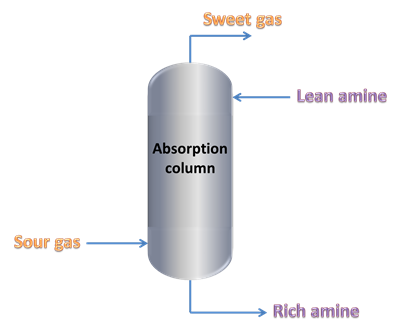
It is a mass transfer process in which a gaseous mixture is put in contact with a solvent in order to eliminate or reduce the concentration of acidic components in the gas to obtain a product that meets the desired specifications. The gas sweetening process is carried out in an absorption column which is represented as follows, where a sour gas, sweet gas, lean amine and rich amine are involved as shown in the image.
Why should the gas be sweetened?
- Safety reasons: Due to H2S toxicity that affects the health of the operating personnel, even causing death; environment and the useful life of equipment and pipes.
- Improve the calorific value of gas: By reducing the content of acid components improves the calorific value of the gas.
- Reduce corrosion: Acid gases when dissolved in water form highly corrosive acids that attack the metallurgy of the equipment.
- Acid gas enrichment: Improves gas quality and its economic value.
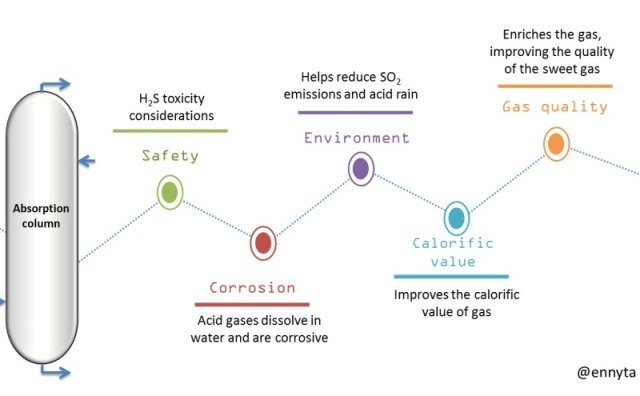
Benefits of the gas sweetening process in an absorption column [Design created by the author @ennyta]
It is important to explain how the operation of the absorption column is to carry out gas sweetening. The column is fed by the bottom with a stream of sour gas and by the top with lean amine, these two phases come into contact in the trays and it is there where the transfer of H2S takes place from the gas phase to the liquid phase, obtaining by the top is a sweet gas and on the bottom an amine rich in H2S.
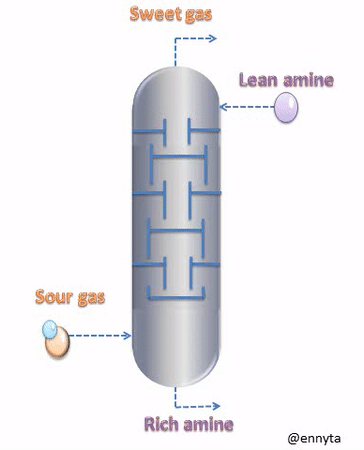.gif)
Representation of the process of absorption of H2S with amine (gas sweetening) in absorption column [Design created by the author @ennyta]
How is amine entrainment identified?
the main problem presented by the absorption column is the amine entrainment, to identify this problem. The Aspen Process Explorer was used as a tool, which is a tracking software to monitor variables in a specific time and identify the amine entrainment event by increasing the level percentage in the fuel gas drum.
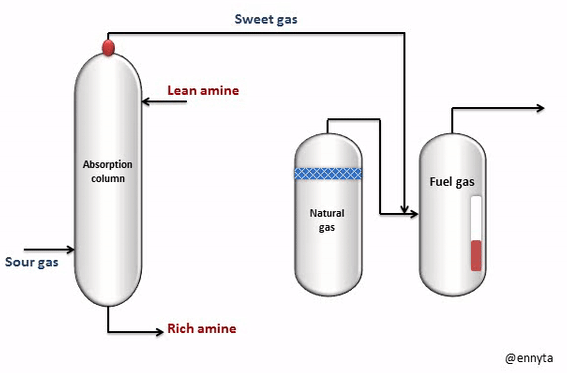.gif)
Representation of the amine entrainment from the absorption column to the fuel gas drum [Design created by the author @ennyta]
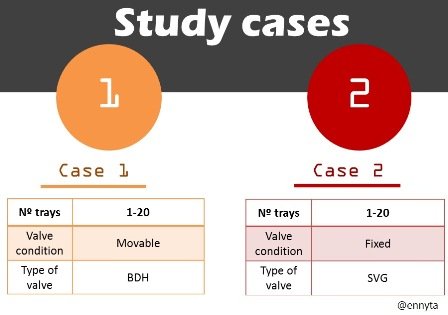
For the evaluation of the absorption column with amine both in its original state and for its new adaptation, 2 case studies were established: CASE 1 where the column consists of plates with movable valves and CASE 2 where these valves were fixed to open position.
How were the hydraulic limitations determined?
For this, the PRO / II process simulator was used for the compositional analysis and the Sulcol simulation package to perform the hydraulic analysis. The hydraulic analysis was based on:
Flooding: It is the excessive accumulation of liquid inside the column and causes an excessive increase in the pressure differential and increases the amount of liquid that descends downcomer.
Weeping: This problem arises when the gas flow with respect to the liquid is so low that the liquid in the tray begins to drip down the perforations towards the lower tray.
D.C. Froth Backup: This problem is related to a flood occurring in the downcomers, which has as a consequence a high pressure drop in the downcomer and eventually the flooding of the tray.
Blowing: The loss of the seal on the tray occurs when very little liquid flows through it, causing the gas to rise through the downcomer instead of rising through the perforations, this generates a decrease in the efficiency of the column.
All these limitations defined by the PDVSA standards as causes that reduce the efficiency of plate columns.
How to determine the efficiency of the absorption column with amine?
To know the absorption efficiency, the following equation was used:

In the equation we consider the concentration of H2S in the maximum sweet gas that the gas can reach to respect the environmental regulations of 0.02 mol% with respect to the concentration of H2S in the real sweet gas obtained during the operations for the case studies.
Alternatives to improve the process of gas sweetening according to the hydraulic limitations presented
A sensitivity analysis was carried out in order to determine the optimal response to the change of some data such as the feeding flow, the concentration of amine and the tray to be used.
Optimal feed flow ratio: Charts were created for the different concentrations of MDEA, on the abscissa axis the acid gas flow is reflected and on the axis of the ordinates in poor amine flow necessary to reach an efficient absorption of H2S in the gas. The obtained curves were adjusted by the linear trend to obtain the equation that will describe the result of the optimal flow relation.
Diagram of operation: Amine and gas flows were varied until reaching the limits to which hydraulic problems arose. A flood of 70%, a downpipe fill of 50% was taken as a limit, for seal loss a minimum value of 0.25 inches and for whining a minimum value of slot factor 0.9 and 0.3 inches of H2O for the pressure drop of the dry plate. All these limits established by the PDVSA standards and suggested by the Sulcol simulator.
Results and Discussion
Operating conditions
The results of the operating conditions in contrast with the design showed that the flow was the parameter that most impacted its deviation. Case 1 obtained the highest percentage of error, greater than 30% for both the gas for the amine (image 1). This depends mainly on the power load that the unit receives; the graph shows that case 1 received less load compared to the other case (image 2).
![]() | ![]() |
Amine entrainment
In relation to the amine entrainment, case 2 presented 29 events and case 1 presented 39. The largest trawl was delineated in red, case 1, for example, operated with a high gas flow, but with a flow of amine very low. The flow relation was not correct, so there was a significant drag in relation to the high flow of gas that carried the liquid with it in its upward trajectory. However, case 2 operated with a flow of amine and gas, both similar to the design conditions and even then an important amine entrainment was observed; When analyzing this, it becomes evident that when operating at flows similar to the design conditions, the column presents hydraulic alterations.
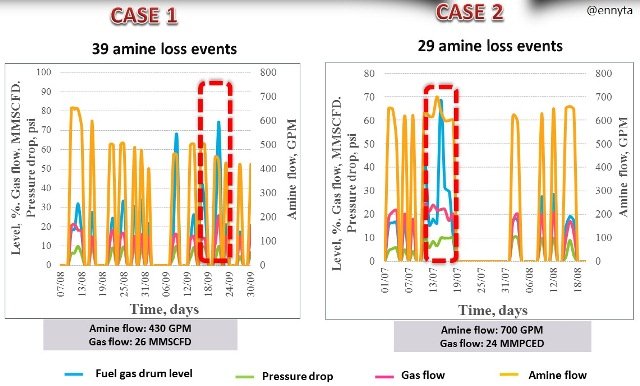
Amine entrainments registered during the absorption column operations [Design created by the author @ennyta]
Hydraulic limitations
The feeding flow was evaluated both for a maximum and minimum flow, according to results, for both cases the flood was acceptable within the 70% limit, the same for the loss of seal, while for the D.C. Froth Backup, for a flow maximum, both for trays with movable and fixed valves, values above 50% were reached, so operating at conditions similar to the design could be the cause of the problem of amine entrainment. On the other hand, the fixed valve tray for minimum flow conditions presented a severe whining problem, while the movable valve plate operated in a normal manner.
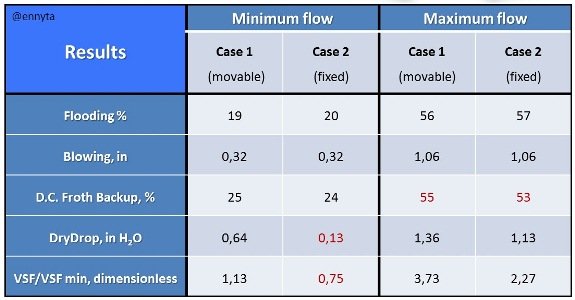
Results obtained from the hydraulic analysis [Design created by the author @ennyta]
Efficiency of absorption of H2S in the gas
Case 1 reached an efficiency of 67.3%, while case 2 achieved an efficiency of 59.2%. According to results, both cases did not comply with the environmental regulations of Venezuela.
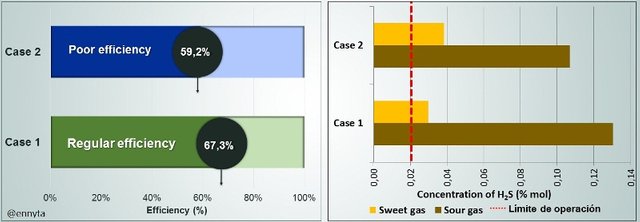
Results obtained from the efficiency of absorption of H2S in the gas [Design created by the author @ennyta]
Alternatives to improve the sweetening process
According to the results, it was shown that the movable valve plates are adequate to minimize the whining problem, while the fixed valve plates have advantages in terms of the problem of valve fouling and clogging.
In relation to this problem, the opening of the valve was evaluated as a recommendation for improvement alternatives. The hydraulic analysis showed that it is more favorable to operate with a valve opening of 70%, that is, to weld the valve to an opening of 0.30 inches and not to 100% as it was done, this in order to minimize the problem of whining that affects the efficiency of absorption of H2S in the gas.
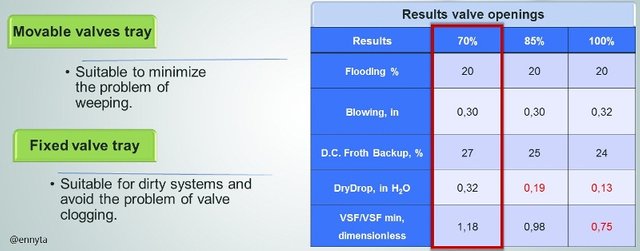
Results hydraulic analysis for valve opening of the absorption column tray [Design created by the author @ennyta]
Optimum flow ratio
An alternative to improve the sweetening process is to operate with an optimal feed flow ratio. In the graphs, the flow of gas and amine with which the column should operate according to the corresponding MDEA concentration can be estimated. For example: for a concentration of 45% MDEA and a gas flow of 20 MMSCFD should be operated with an amine flow of 500 GPM. If it is desired to operate with the same gas flow, but at an amine concentration lower than 35%, it is necessary to consider increasing the amine flow to 640 GPM to guarantee a good sweetening process.
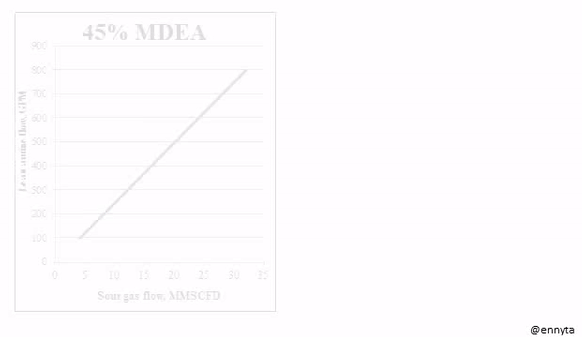.gif)
Graph to determine the correct feed flow ratio for a MDEA concentration of 35% and 45% [Design created by the author @ennyta]
Diagram of operation
The operation diagram is another improvement alternative in which hydraulic problems that could occur if not operated with correct flows are observed. For example, with the previous flow ratio, the column is expected to operate under normal conditions, but if 400 GPM of amine is operated and a gas flow of 25 MMSCFD, seal loss will occur and, therefore, a carryover will occur. liquid to the upper tray.
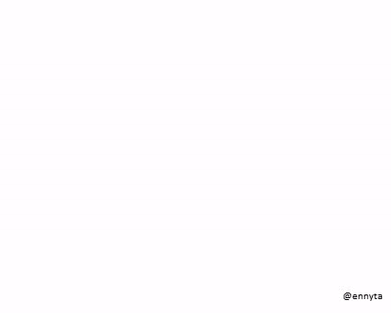.gif)
Graph to determine the correct feed flow ratio to avoid hydraulic problems [Design created by the author @ennyta]
Conclusions
Case 1 showed a greater percentage of deviation in the feed flows due to the low load to the delayed coking unit.
Case 1 presented the highest number of amine entrainment.
For flows similar to the design conditions, there is a high percentage of filling of the downcomer and, consequently, possible problems related to the amine entrainment.
Case 2 with valve opening at 100% is more prone to presenting the phenomenon of weeping.
Case 2 obtained the lowest efficiency percentage of H2S absorption in the gas with 59.2%.
Fixed valve tray with a welded valve opening at a height of 0.30 inches, ie 70% opening, was considered to be the best mechanical adaptation.
Recommendations
Maintain good quality and flow ratio in the feed streams to avoid problems during the gas sweetening process.
Do not saturate the rich amine above 70% of its equilibrium capacity as it can cause corrosion problems.
Lean amine temperature should be maintained slightly above the sour gas temperature to avoid condensation of the hydrocarbons. It is recommended that it be 10 ° F warmer.
To avoid the problem related to the amine drag, it is recommended:
- Install a mist eliminator at the top of the column to avoid dragging related to foam formation.
- Install a gas separator treated downstream of the column to recover the lost amine from the system.
- Install activated carbon filters before the column to remove the solids from the poor amine.
- Install an anti-foam injection system in the column to avoid the formation of foam, promoter of the amine trawls.
Information taken from thesis - paper by Ennyluz Cordero (@ennyta):
Cordero, E. Evaluación de las condiciones operacionales de la columna de absorción con amina, perteneciente a la unidad de coquificación retardada del mejorador Petropiar. Thesis. Department of Petroleum Engineering. Universidad de Oriente, core of Anzoategui. Barcelona, Venezuela. (2017).
upvote for me please? https://steemit.com/news/@bible.com/6h36cq