Post-Processing a 3D Printed Dragon Part 4: Filling in the model gaps
Alright, finally part 4 into this series!
Last time we ended with all of the model halves glued together. This time, we get to deal with one of the byproducts of that: the model gap.
[picture of model gap]
A model gap is pretty much exactly as it sounds - an air gap between parts of the model. In my case this gap was the area between the halves that I glued together.
Now, leaving the gap in would've been fine since sometimes it doesn't usually hurt the model aesthetically, but I wanted to see if I could do something about it.
And lucky for me, there is a way to deal with these gaps! Turns out there's this stuff called modeling putty that's made exactly for this reason - you fill in the gaps, let it dry, sand off any remainder and away you go.
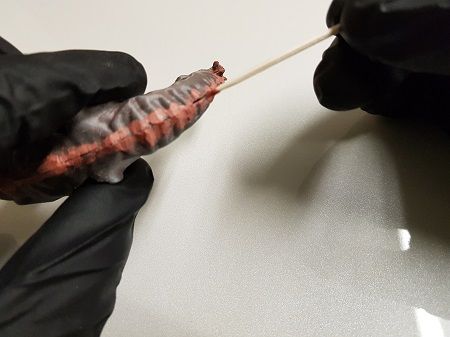
And here it is initially applied to each piece:
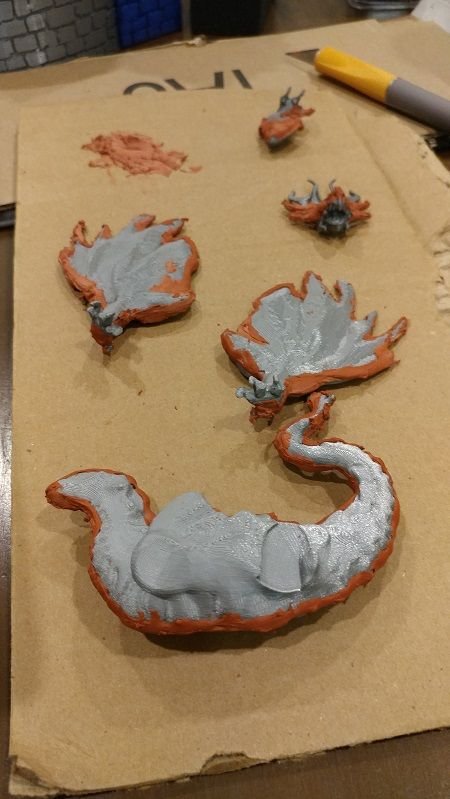
And after that was sanded down a bit:
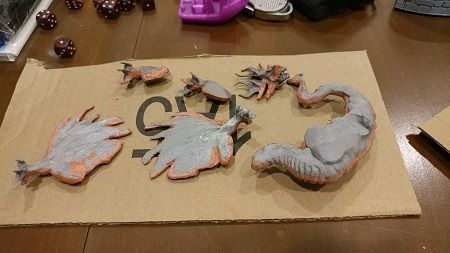
The only issue I ran into was that some of the putty didn't fill in correctly and actually fell out of the gaps when I trimmed/sanded the putty down:
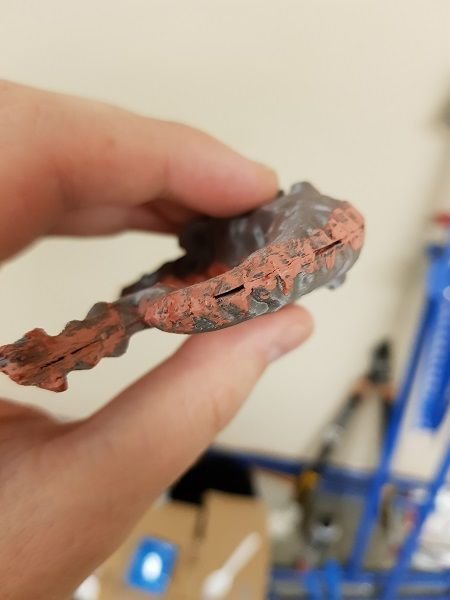
So I had to fill those gaps in again and re-sand. Not that difficult to do, but still something to watch out for.
So far I'm liking how this model is turning out! Next up will be the start of priming/painting, so look forward to that!
Previous Parts:
Part 3: Gluing the halves together
Part 2: Trimming and De-warping
Part 1: The print
model looks brilliant excellent work :)
Thanks!
Congratulations @xerdo! You have received a personal award!
_Click on the badge to view your Board of Honor.
Congratulations @xerdo! You received a personal award!
You can view your badges on your Steem Board and compare to others on the Steem Ranking
Vote for @Steemitboard as a witness to get one more award and increased upvotes!