Analyzing the applications of reinforced fiber polymers
Reinforced fiber polymers; properties and applications.
A reinforced fiber polymer is a composite material consisting of a polymer matrix embedded with high strength fibers. In general, the polymer matrix is a thermoset plastic, such as unsaturated polyester or epoxide, but thermoplastic polymers are also used, such as nylon (polyamides), polycarbonate, polystyrene and polyvinyl chloride. In addition, elastomers are also reinforced with fibers for rubber products such as tires and transported belts.
The fibers of the CMP take different forms: Discontinuous (in pieces), continuous or woven like cloth. The main fiber materials in FRP are glass, carbon and Kevlar 49. Boron and steel are among the least common fibers. Glass (particularly E glass) is the most common fiber material in today's FRP; its use as a plastic reinforcer dates back to 1920, approximately.
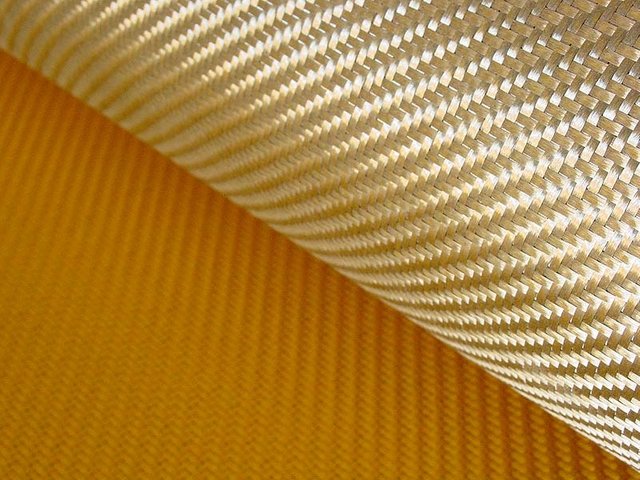
Kevlar 49
Source
The term advanced compounds are sometimes used in relation to the FRP developed from the end of the 1960s and that use boron, carbon or Kevlar as reinforced fibers. The most common polymer matrix is epoxy. These compounds, in general, have high fiber content (more than 50% of the volume) and have high strength and modulus of elasticity. When two or more fiber materials are combined in the FRP compound, it is called a hybrid compound. The advantages of hybrids over conventional or advanced FRP include the balance between strength and stiffness, improved toughness and impact resistance, and reduced weight. Advanced compounds and hybrids are used in aerospace applications.
The most used form of the FRP is a luminous structure, made by stacking and bonding thin layers of fiber and polymer until the desired thickness is obtained. By varying the orientation of the fibers between the layers, the level of anisotropy specified in the properties of the laminate is achieved. This method is used to form thin cross-section pieces such as wing and aircraft fuselage sections, car and truck body panels, as well as ship hulls.
Properties.
There are a number of attractive features that distinguish fiber-reinforced plastics among engineering materials. The most notable are:
- High resistance to weight ratio.
- Large weight module ratio.
- Low specific gravity.
A common FRP weighs only one-fifth that of steel, but its strength and modulus are similar in the direction of the fiber. The following table compares the properties of several FRP, sheets of steel and aluminum alloys.
a- The indices are stress-weight resistance ratios (TS / SG) and elasticity-weight modulus (E / SG), compared to steel at low C (index = 1.0 for the base).
b- In the FRP, carbon fibers with high tensile strength are used.
c- High modulus carbon fibers are used in the FRP.
The properties that are listed in it depend on the proportion of fibers in the compound. Both the tensile strength and the elastic modulus increase as the fiber content increases, according to the following equation:
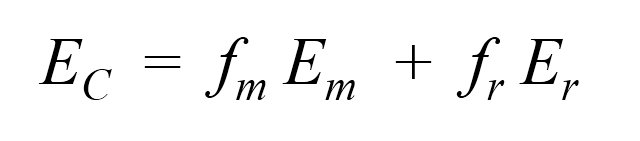
Other properties and characteristics of reinforced fiber plastics include:
- Good resistance to fatigue.
- Good resistance to corrosion.
- Low thermal expansion of many FRP, leading to proper dimensional stability.
- Significant anisotropy of its properties.
In relation to the last characteristic, the mechanical properties of the FRP that are given in the table, are in the direction of the fiber. As you said, when measured in a different direction, their values are significantly lower.
Applications.
During the last three decades, there has been a sustained growth in the application of fiber-reinforced polymers in products that require high strength and low weight, often as metal substitutes. The aerospace industry is one of the largest users of composite materials. Designers continually strive to reduce the weight of aircraft in order to increase fuel efficiency and load capacity. The applications of composite materials in both military and commercial aviation have grown steadily. Much of the structural weight of today's aircraft and helicopters consists of FRP. The following image identifies the compounds used in the Boeing 757.
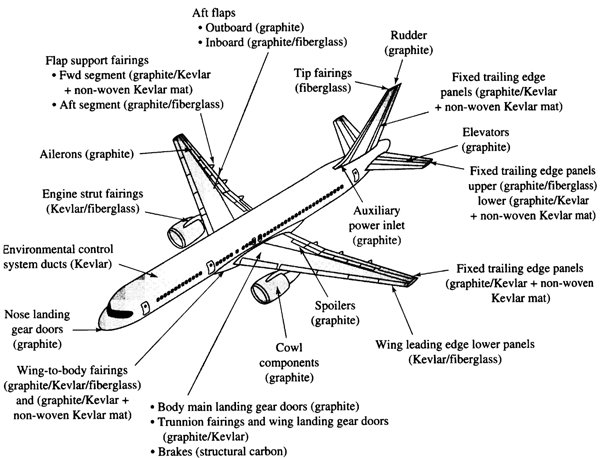
Source
The automotive industry is another important use of FRP. The most obvious applications of FRP are in body panels of cars and trucks. A notable example is the Chevrolet Corvette, which for decades has been produced with FRP bodywork. In certain chassis and part of engines, there are less obvious applications. Automotive applications differ from those of the aerospace industry in two significant aspects. First, the requirement of a high weight-resistance ratio is less demanding than on airplanes. Truck and truck applications use conventional fiberglass reinforced plastics instead of advanced composites. Second, the production quantities are much higher in automotive applications, which require more economical manufacturing methods. The continued use of low carbon steel sheets for automobiles despite the advantages of FRP is evidence of the low cost and ease of processing of the steel.
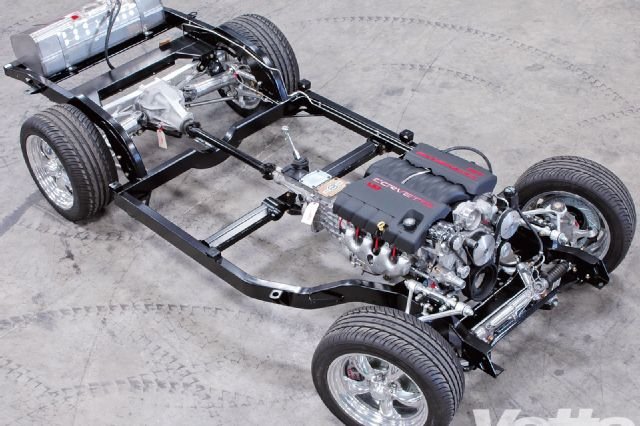
Source
FRPs have been widely adopted for recreational and sports equipment. Fiberglass reinforced plastic has been used for boat hulls since the 1940s. Fishing rods were another early application. Today, FRPs are represented in a wide range of sports products, including tennis rackets, golf clubs, football helmets, bows and arrows, skis and bicycle wheels.
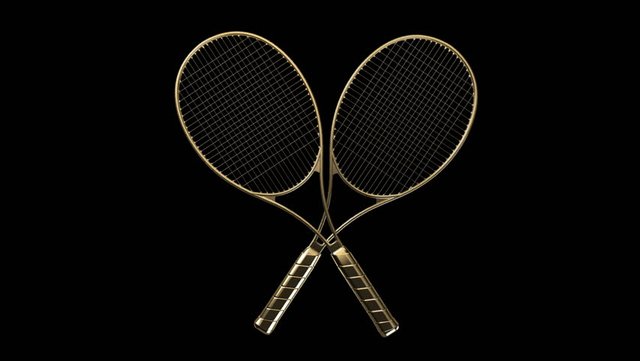
Source
References:
- https://www.intechopen.com/books/fiber-reinforced-polymers-the-technology-applied-for-concrete-repair/introduction-of-fibre-reinforced-polymers-polymers-and-composites-concepts-properties-and-processes
- https://www.thoughtco.com/properties-of-frp-composites-820515
- http://www.aml.engineering.columbia.edu/ntm/level1/ch05/html/l1c05s03.html
- Manufacturing Processes for Engineering Materials, by Serope Kalpakjian
- Introduction to Manufacturing Processes, by Mikell Groover
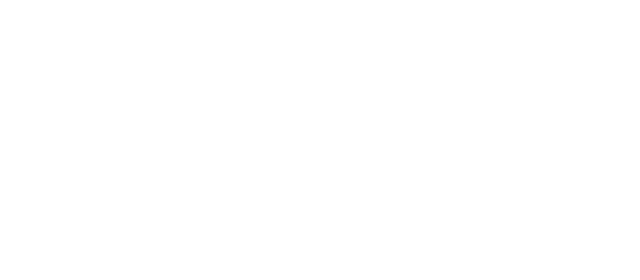