Understanding Corrosion, It's Control And Prevention
The use of metal in today's world cannot be over emphasize, as basically almost all engineering infrastructures are composes of one metal or the other or an alloy of metals. The lifespan of these structures lies on the strength of the materials used, of which metal or alloy is also involved. To maintain the strength of a material and increase it lifespan, the concept of corrosion must be fully understood, i.e it's types, prevention and control mechanisms, as corrosion is responsible for the deterioration, loss of strength and finally failure of most engineering materials. Although corrosion is applicable to any kind of material, this work will be focusing more on corrosion of metal and that of its alloys.
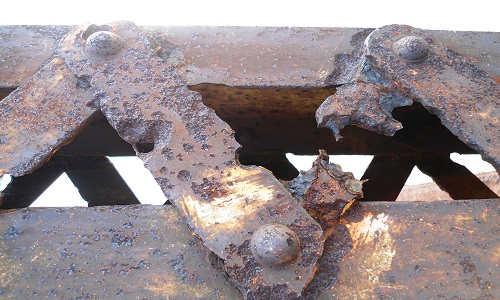
The term corrosion is defined as the deterioration of a material due to its interactions with the environment. This interaction in metals is an electrochemical reaction that causes changes to both the metal and the interacting surrounding. The rate of corrosion differs with materials and also dependent on factors such as the environmental conditions and the prevalent gases in contact with the metal. There are approximately eighty (80) known metals in the one hundred and five (105) chemical elements known, these metals can be combine at different conditions to form alloys of different properties. There are over forty thousand (40,000) different alloys known today and these alloys differs in their physical, chemical and mechanical properties, these difference in properties causes a slight or large variance in their rate of corrosion.
In nature, almost everything fight to return to it's original state, a state of stability and low energy requirement, this is same for engineering materials such as metals and alloys. Metals are found as compounds with other elements, except copper and precious metals such as gold, silver, platinum, etc which have oxidation state greater than zero. Other metals posses zero oxidation states, but are not used in these states, therefore they undergo a process called smelting, i.e a process of adding great amount of energy to the metal in form of heat. Metals tends to return to it stability states when expose to its environment, this process of losing energy to environment is corrosion. It is a redox reaction, i.e it is involve a cathodic and anodic reaction.
As established above, corrosion is an electrolytic reaction, i.e it is a reduction-oxidation reaction. By oxidation we refer to the loss of electron in a region referred to as anode while reduction is the gain of these electron in the region referred to as cathode. There are three major/necessary components that must be present for corrosion to occur, these are the metal, oxygen from the atmosphere and water or moisture as the case may be. In corrosion, the metal acts as the anode, its reaction with the environment causes it to oxidized, producing both metal ions and electrons. The electrons reduce the oxygen most times to form hydroxide alongside a complimentary cathodic reaction. There are two basic outcome from the dissolution of the metal at the anode; firstly is the metal ions forming a solid compound at the surface, leading to the formation of a protective barrier and the collection of solid metal ions which can inhibit further corrosion, secondly is the metal ion going into the solution forming an hydrated, this can lead into formation of an open pit as a result of further oxidation of metal ions.
Rusting as a Corrosion Process
Using corrosion in iron as a case study for this work, several people have mistaken corrosion for rusting, thou they both involve deterioration of metals as a result of interaction with environment. Rushing is a process of corrosion involving iron, i.e the corrosion of a material that contain iron. Rusting is a chemical process that involve the reaction of iron with oxygen in the presence of water or moisture to form iron-oxide. This iron-oxide forms a reddish-brown color compound known as rust. Rushing doesn't take place in iron alone, it also present in alloys of iron. Rusting doesn't stick to one spot as it spread till the entire metal is affected and disintegrated.
The chemistry behind rusting of iron is the migration of electron from the iron atom to form a bond with oxygen giving rise to hydrated iron (III) oxide (Fe2O3·nH2O) and iron (III) oxide-hydroxide (FeO(OH), Fe(OH)3. As established already, metals including iron goes through a process of heating known as smelting after which this metals are cooled base on the desired properties and structures. For manufacturing of iron, during the cooling stage, two micro structures are formed namely pearlite and ferrite. During corrosion of iron, the pearlite acts as the cathode while the ferrite acts as the anode. Corrosion normally take place at the anode (ferrite region) while rust (reddish-brown color compound) as a product of the corrosion is formed at the cathode (pearlite region).
The equations involve in rusting
The Iron atoms releases two electrons from the ferrite region and form iron (II) ions.
Oxidation Half Reaction;
In the presence of water, the Oxygen atom accepts the release electrons to forms hydroxide ions.
Reduction Half Reaction;
Combining both equations;
Further reactions results in;
The Fe(OH)3 formed dehydrates to form the product of corrosion, i.e rust
The general formula for rust is
While the general equation for rust is;
Factors Affecting The Rate of Corrosion
Before going into prevention mechanisms for corrosion, it is important to know some basic factors that can promote corrosion in metal, below are some of these factors;
Temperature; The rate of corrosion increases with increase in temperature, it has been proven that if corrosion rate is only controlled by metal oxidation process, the corrosion rate follows an Arrhenius relationship, i.e the rate of corrosion increases exponentially with increase in temperature. Also according to Thumb's rule, when temperature is increase by 10oC, the rate of corrosion is double.
Concentration; The concentration of the metal or alloy determines the rate at which it will corrode. Increase in concentration will cause an increase in corrosion rate, this continues until maximum level is attain, after which further increase has no effect in the rate of corrosion.
Oxidizing Agents; Corrosion is a redox reaction, i.e it involve both anodic and cathodic reaction spontaneously, this reaction continues because of the presence of oxidizing agents. Restricting oxidizing agents from these metals will reduce or stop corrosion completely.
The electric conductivity of the electrolyte; Corrosion is an electrochemical reaction, i.e it involve electrolyte, therefore the electrical conductivity of the electrolyte has an effect on the rate of reaction. Increasing the electrical conductivity of the electrolyte will increase corrosion rate, therefore substance such as salt presence which increases electrical conductivity will cause an increase in corrosion rate, this is the reason metal corrode faster in salt water than in fresh water.
Prevention Of Corrosion
At every stages of an engineering project, corrosion must be checked to avoid losses and danger to life and resources, some of the prevention methods are discussed bellow;
Painting; This is a very effective method of preventing corrosion as metals interact with environment to corrode. Painting serves as a layer of protection between metal and the environment, this prevention of interaction therefore prevents the metal from corrosion.
Sacrificial Anodes; The use of sacrificial anode involve using a highly active metal to prevent a less active metal from corroding, this highly active metal is a metal alloy with a more negative electrochemical potential from the one it is coating, therefore electrical current will flow more readily from this newly introduced metal. The introduced metal is sacrifice for the less active metal.
Cathodic Protection; This is a method of protecting metals from corroding by using a surface to act as the cathode of an electrochemical cell.
Passivation; This is another process of preventing corrosion by creating conditions that favors some corrosion processes that are less destructive to the metal. One of such corrosion processes is one in which the initial metal corrosion creates solid metal compounds that will act as coat to the initial site and prevent further corrosion.
Conclusion
The effect of corrosion cannot be undermined in both industries and our neighborhood. Corrosion caters for a huge amount of damages in most engineering material, most especially metals. To reduce these losses of materials and danger to man as pose by corroding metals, there is need for all not just engineers to understand corrosion, how it works, factors that promote it and how it can be prevented. With this knowledge at hand, we can reduce corrosion to the barest minimum and therefore increase the lifespan of infrastructures and machinery, making our environment less polluted with scraps from rusted metals.
I am really impressed with the content of your post. I like the fact that you made it comprehensive enough.
Corrosion is an inevitable parasite that has plagued every aspect where one form of material or the other is involved and we can only hope to find the best way to minimize its impact.
However, I will like to point out that Sacrificial anode is one type of cathodic protection (as you have noted) with impressed current being another. Painting, galvanizing and formation of allow should not be considered as types of cathodic protection. In fact, pure metals have superior corrosion resistance than alloys.
The counterpart of cathodic protection is anodic protection which harnesses the phenomenon of passivity.
I hope you don't mind my contributions. Great Job by the way.
Wow
Thanks for dropping by and also airing your view, thats the beauty of steemsteem community.
Regarding your observation;
These method can also be referred to as cathodic protection according to this referenced material
https://chem.libretexts.org/Core/Analytical_Chemistry/Electrochemistry/Exemplars/Corrosion/Sacrificial_Anode
I understand you have a source for the information, but know that not all you see online is correct.
I understand you have a source for the information, but know that not all you see online is correct.
Congratulations! This post has been upvoted from the communal account, @minnowsupport, by gtan from the Minnow Support Project. It's a witness project run by aggroed, ausbitbank, teamsteem, theprophet0, someguy123, neoxian, followbtcnews, and netuoso. The goal is to help Steemit grow by supporting Minnows. Please find us at the Peace, Abundance, and Liberty Network (PALnet) Discord Channel. It's a completely public and open space to all members of the Steemit community who voluntarily choose to be there.
If you would like to delegate to the Minnow Support Project you can do so by clicking on the following links: 50SP, 100SP, 250SP, 500SP, 1000SP, 5000SP.
Be sure to leave at least 50SP undelegated on your account.
Corrosion is truly a menace to metals and if not properly managed, can cause devastating effects. I actually did a project on cathodic protection and I might have to share sometime.
Nicely written!
Thanks for your contribution, looking forward to your post